Sealcoating is a crucial part of asphalt maintenance. It protects against harsh weather conditions and preserves the blacktop’s appearance.
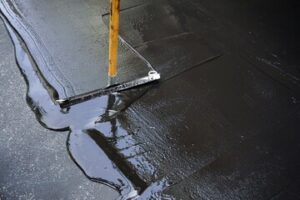
It’s important to choose the right application method for each job. Spraying is faster than squeegee application and can produce a smoother finish. Visit https://www.rochesternysealcoating.com/ to learn more.
Before applying any sealcoat, workers must clear the pavement and remove all vehicles. This is because cars and trucks can scratch or dislodge the sealer.
A properly installed asphalt sealcoat can protect a paved surface from oxidation, weathering, and chemical damage. It also helps to fill cracks and small holes, making the surface smooth and enhancing its appearance. It is an affordable option for homeowners and business owners that wants to add value to their property. However, it is important to understand that seal coating is not a replacement for paving and repairs should be done regularly to keep the pavement in good condition.
The cost of a sealcoating job depends on several factors, including the type of sealcoat used and the current condition of the pavement. Most sealcoating jobs will require a few hours to dry, so workers must be able to work quickly. It is also essential that the weather conditions are ideal for applying a seal coat. The temperature must be above 50 degrees, and there should be no rain in the forecast for 24 hours.
There are a few different types of sealcoats, and each has its own advantages and disadvantages. Coal tar is the most common and economical, but it doesn’t last as long as other options. Asphalt emulsion is similar to coal tar, but it’s better for commercial applications because it can be applied to surfaces that are not suitable for coal tar. However, it’s not as durable as other options and may need to be reapplied sooner.
Another popular option is acrylic sealcoat, which is available in a variety of colors and provides the most durability. It also comes in a water-based formula and is less toxic than other products. This sealcoat is usually less expensive than coal tar, but it’s still more costly than asphalt emulsion.
Before beginning a sealcoat project, workers must prepare the surface by sweeping and clearing any dirt or debris. They also need to mask off any areas that shouldn’t get coated, such as curbs and gutters. If the work area is not well prepared, the sealcoat will crack and peel off.
A sealcoating project can be a big investment, but it will save you money in the long run by protecting your pavement from further damage. Without proper maintenance, the asphalt can become cracked and pitted, which can lead to tripping and falling accidents. It can also cause serious damage to vehicles. This can result in costly repair bills for both the vehicle and the owner of the property.
Longevity
A typical sealcoating will last between two and five years, but the lifespan can vary greatly depending on the quality of the materials used and the application process. The best way to increase the longevity of a sealcoat is to work with a professional who uses high-grade products and proper application techniques. This will ensure that the coating is thick enough to provide effective protection from harsh weather and other elements that damage asphalt surfaces.
The type of pavement and traffic volume will also affect the longevity of sealcoating. For instance, high-traffic areas will wear down the surface more quickly due to mechanical abrasion, which can cause larger cracks and potholes. This can also lead to the need for more frequent resealing.
Another factor that can affect the longevity of a sealcoat is its exposure to sunlight. Over time, UV rays can break down the material and make it more brittle. The oxidation of the asphalt beneath the sealcoat can also accelerate the breakdown. In order to maximize the lifespan of a sealcoat, it is important to apply it properly and keep up with regular maintenance.
Regular sweeping is critical to the longevity of an asphalt surface. It helps to remove debris and oil stains that could otherwise cause the sealcoat to degrade more quickly. It is also recommended to pressure wash the surface every year in areas that are prone to mildew or other contaminants. In addition, it is important to avoid sealing areas that are already damaged or cracked. This will help to minimize the amount of material that is displaced and allow the existing cracks to repair themselves. A thorough cost-lifespan analysis should take traffic, weather, and maintenance schedules into account to determine the best approach for a cost-effective sealcoating project.
Environment
One of the most important reasons to sealcoat is because it protects your asphalt from environmental damage. When you don’t sealcoat your parking lot, water seeps into the cracks and holes, which erodes at the graded foundation that supports your pavement and accelerates the deterioration of the asphalt surface itself. Sealcoating prevents this by filling in the cracks and blocking out the water, keeping your asphalt looking like new for years to come.
There are several types of tar used in sealcoats, including refined coal tar, asphalt emulsion and fast-drying oil-based types. Each type has its own advantages and disadvantages, but refined coal tar is the most common and the best option for your parking lot. It dries quickly, resists the elements and lasts for up to seven years. It’s also environmentally friendly, since it doesn’t contain any petroleum products or salts.
Coal tar-based sealcoats release polycyclic aromatic hydrocarbons (PAHs) when they’re applied, curing and weathering. These compounds can contaminate soils, dust and waters. PAHs are carcinogenic, and repeated exposure can cause cancer in animals and humans. They can also cause birth defects and death in fish, insects and other organisms.
Workers must follow strict safety guidelines when applying a seal coat, and they must wait 24 hours to let the seal coat dry before cars can be driven on it. They must also use barricades and warning tape to keep people away from the area during this time. Workers must wear protective equipment and be careful not to get the tar on them.
The chemicals used in coal tar-based sealcoats can be harmful to the environment and human health, especially if they come into contact with it on bare skin or lungs. These chemicals can have long-term health effects, and may even lead to respiratory problems in sensitive individuals.
The main reason for a negative environmental impact from sealcoating is the toxicity of the coal tar emulsion. These chemical compounds can leach into the groundwater supply and contaminate rivers and lakes. They also contaminate the air, and can make their way into homes through shoes or clothing. In addition, the vapors from coal tar can be irritating to eyes and lungs.
Safety
While the risk of injury or damage is minimal if you’re working on your own driveway or parking lot, applying sealcoat is still hazardous work. The fumes can be irritating to the nose and throat, and the chemicals used to mix the coating are toxic if ingested or inhaled. Workers need to take special precautions when it comes to safety, particularly if they’re applying the coating in extreme heat. They should also wear personal protective equipment, such as gloves and eye protection.
There are several different types of coatings available to homeowners, including coal tar, asphalt emulsion, and acrylic. Refined coal tar is the most common and is often marketed as “green” because it’s less toxic than other materials. However, it’s important to note that coal tar has been linked to cancer and other health problems. It also contains petrochemicals, which can leach into waterways and cause environmental concerns.
Asphalt emulsion is a more environmentally friendly option, but it’s not as strong as coal tar and can’t be used on all surfaces. It’s better suited for use on driveways, and it can last up to seven years before it needs to be replaced. Acrylic is the most expensive coating, but it’s durable, UV resistant, and available in a variety of colors. It’s also easy to apply and provides excellent traction.
The final consideration when it comes to sealcoating is safety. Without sand, the pavement becomes slippery, and pedestrians can easily slip and fall. This can lead to injuries and lawsuits against property owners. Adding silica sand improves the surface’s traction and helps prevent accidents and injuries. It also reduces glare from bright sunlight, making it safer for drivers.
Contractors should always follow the manufacturer’s instructions when mixing their sealcoating. They should not add too much sand, because it will make the mixture too runny and it won’t flow properly. They should also avoid using coarse sand, because it will not be held well by the sealcoat and will likely be knocked off by passing vehicles. The sand should be sieved to ensure that it’s not too fine or too coarse. The proper sizing will also help the mixture to adhere well to the pavement.