Phoenix 3D Printing is the layer-by-layer fabrication of physical objects from a digital 3-dimensional model. This includes both rapid prototyping and on-demand manufacturing.
Printing on-demand allows companies to manufacture near their customers, cutting transportation costs and tariff risks. It also cuts inventory costs and shortens design and production cycles. It is also environmentally friendly and uses sustainable materials.
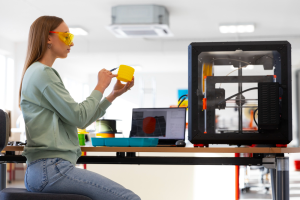
The 3D printing process allows companies to prototype physical models of computer aided design (CAD) data, shortening the development cycle and allowing for iterations. Using this method, a designer can go from idea to having a prototype in his hands within days. The shortened time frame also allows for users or focus groups to give feedback, and it helps designers spot problems early. The resulting prototypes are often much better than the final product as they have had multiple rounds of testing, but still cost a fraction of traditional production methods.
One major benefit of rapid prototyping is that it increases stakeholder buy-in. The ability to show the progress of a project, and the fact that stakeholders are able to see the physical representations of their ideas, results in higher levels of engagement than would otherwise be possible with other methodologies. This can significantly reduce the number of revisions required before a successful final product is delivered to paying customers and prospects.
Rapid prototyping is used to create a range of different types of prototypes, depending on the intended application. Proof-of-concept prototypes are the simplest and most commonly used, providing a quick visual representation of a concept. They are typically created using low-cost, easy-to-use processes such as 3D Printing or CNC machining, and are used to assess the feasibility of an idea before investing in more detailed development.
More advanced prototypes are used for functional testing, and can be created from a variety of materials and manufacturing techniques, such as metals (used in Selective Laser Melting and Direct Metal Laser Sintering), plastics (such as PET and PVC, ABS, and PLA), ceramics, and resins (used in Stereolithography and Digital Light Processing). Prototypes created with these different processes vary in their strength, durability, and surface finish.
Businesses can use the rapid prototyping process to produce end-use parts and products, as well as tooling, jigs and fixtures. This can cut costs by eliminating the need for costly injection molds and reducing the time it takes to move from prototype to production. It can also allow for on-demand manufacturing, reducing inventory and enabling companies to respond quickly to customer demands.
Rapid Manufacturing
During rapid manufacturing using 3D printing technology, a digital design of a product or part is sent to a printer, which creates the physical replica in various materials, such as plastic or metal. This process replaces traditional methods that require a significant amount of time to fabricate prototypes, and it provides businesses with a fast path from concept to finished product.
This type of production is ideal for prototyping and small-run manufacturing, since it allows designers to iterate on a design until they achieve the desired result. It also enables companies to cut costs and shorten lead times, which is crucial when it comes to competing with larger competitors in the same market.
One of the primary benefits of rapid manufacturing is that it reduces material waste, especially when compared to subtractive processes such as CNC machining. This is because the 3D printing process only uses as much material as it needs to produce the final object, layer-by-layer. This eliminates excess material and can save on both raw materials and labor costs.
Another advantage of rapid manufacturing is that it allows designers to produce highly complex parts and products. For example, jewelry makers use 3D Printing to create intricate and unique designs that would be difficult or impossible to make with other techniques such as CNC machining and lost-wax casting. This can help them increase their revenue by appealing to a more diverse client base.
While traditional methods still have a place in the industry, there is a growing trend toward using rapid manufacturing for low- to mid-volume productions. This is due to technological advancements, the availability of affordable and high-quality printers, and the benefits that come with associated processes such as hybrid manufacturing.
For example, some of the latest metal printing technologies include direct metal laser sintering (DMLS) and directed energy deposition (DEP). These technologies use a multi-axis robot that deposits wire or powdered metal onto the surface of an object, which is then heated by a laser to melt it into the desired shape. The resulting solid can be used for structural applications and can stand up to the same stresses as traditional manufactured parts.
Design Flexibility
A key aspect of 3D printing technology is that it can produce a part with complex geometries, which were difficult or impossible to create using traditional manufacturing techniques. This design flexibility opens up new possibilities and design freedom for engineers. For example, the flexibility of the process makes it easy to change a design as needed in the prototyping phase, which reduces time and expense and helps to speed up product development. This is also true for the full production of a finished product, which allows companies to adapt quickly to market changes or customer demands.
In addition, the layer-by-layer approach of 3D Printing allows for precision that is not available with other manufacturing methods. This can help eliminate common errors that can occur with injection molding, such as voids and inaccuracies. It can also help avoid issues that can plague CNC machining, such as burrs and poor surface quality.
The flexibility of 3D Printing can also be used to simplify maintenance by reducing the number of parts in an assembly. For example, a component that requires regular replacement can be consolidated into a single print instead of being made in several separate parts and then assemble together. This can lower the overall cost of the part and make it easier to replace.
Another way that 3D Printing can improve maintenance is by incorporating flexible materials. These materials can flex when they are under load, which can protect against damage and stress. They can also be printed with mesh structures that are more dense where stress concentrations are high and less dense where they are low. Techniques like topological optimization and generative design can also help to optimize a part for its specific load case, removing material that won’t provide any structural benefit.
Finally, the flexibility of 3D Printing can help to reduce the environmental impact of manufacturing by allowing businesses to produce closer to their customers. This can lower shipping costs and cut energy usage. It can also reduce the need for worldwide transportation, which cuts greenhouse gas emissions and other pollutants.
Sustainability
Over the past few decades, concerns about the impact of human activity on our planet have increased. Manufacturing activities in particular have been a focus of concern because of the significant amounts of raw materials used and the massive amount of waste they generate. 3D printing technology offers a viable solution to these issues by providing a more sustainable alternative to conventional manufacturing techniques.
3D Printing is a very energy-efficient process. In many cases, only the energy required to heat the printer and material are needed. In contrast, traditional manufacturing processes require a lot of water and use large quantities of energy to produce, transport, and assemble products.
Additionally, using 3D Printing for production enables companies to print parts as they are needed rather than producing large batches and stocking them up in warehouses. This on-demand approach reduces the need for a large inventory, which cuts down on waste and inventory obsolescence.
Misprinted or defective workpieces can also be melted down and used for new prints, reducing the need to obtain new materials. This type of recycling is especially useful with thermoplastic filaments that are able to be reused.
In addition, the durable materials used in 3D Printing often require less maintenance and last longer than their traditional counterparts. For example, 3D printed athletic shoes can last up to three times longer than their foam-based counterparts. This reduced need for replacements translates to reduced landfill waste and energy usage.
Furthermore, many of the materials used for 3D Printing are either recyclable or bio-based. For example, PLA (polylactic acid) filaments are made from renewable resources such as corn starch and coffee grounds. They can even be disposed of in industrial composting plants. Other materials, such as bio-based polymers and metals are being developed to further reduce the environmental footprint of 3D Printing.
In the future, it is likely that 3D Printing will be used to make a number of different components of buildings and other structures. This will not only cut down on construction costs and speed up the building process, but it will also reduce energy consumption and carbon emissions.