Adding a fence to your property can increase safety and curb appeal. It can also mark property lines, protecting pets and children from stray dogs or other neighborhood hazards.
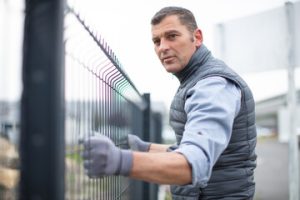
A seasoned fence contractor has refined skills that result in precise installations and sturdy structures that stand the test of time.
Whether you are looking for added privacy, security, or property boundaries, a fence is a great way to enhance your home and protect its value. However, before you get to digging holes and putting up posts, it’s important that you take the time to ensure that your fence will be safe for everyone involved. This begins with taking accurate measurements and ensuring that the location of your new fence adheres to any local regulations. This includes checking for any property easements, observing height restrictions (often 6 feet, but this may vary), and making sure that your fence isn’t encroaching on your neighbor’s land.
The next step in the fence installation process is obtaining any necessary permits and inspections. Many cities require that you obtain a permit before starting construction, so it is important to check with your city’s building department for specific requirements. Depending on where you live, you may also be required to have your electrical work done by a licensed electrician.
It is also a good idea to discuss your fence plans with any adjacent neighbors, as they will likely be affected by the new boundary lines. This can prevent any miscommunication and disagreements that could potentially occur during or after the installation of your new fence. Finally, it is a good idea to remove any obstacles that might obstruct the fence installation. This can include removing tree stumps, branches, rocks, slopes, and other obstructions.
Permits
Before your fence is installed, it’s a good idea to get all your legal ducks in order. Many localities have rules and regulations that must be adhered to, including zoning laws and HOA guidelines (where applicable).
A permit is typically required for any fencing construction. If it’s not, you could face fines. The requirements for obtaining a permit vary from state to city, but will usually involve submitting a site plan that details the proposed fence’s dimensions, materials and location in relation to your property line. Some cities will also require sketches, plans and photographs with your application.
Once your plans are reviewed and approved, you’ll be issued a fence permit. Keep in mind that you may need to contact 811 call-before-you-dig in advance of beginning work, so that they can mark off any underground utility lines before digging starts.
You might also need to get your neighbor’s written consent to build a fence near them. This is especially important in urban areas, where fences can impact your neighbors’ quality of life. Some cities even have rules that prevent you from building a fence that blocks the view of a landmark or historical site. Precisely marking out the fence line before construction begins ensures that your new fence is placed precisely where you want it and minimizes future problems like leaning or warping.
Site Preparation
During this phase, a professional team will prepare the area for fence installation by clearing obstacles and making sure the property lines are marked. This step is vital for ensuring that your fence is built within the boundaries of your property and avoiding any potential issues with neighbors. If you’re not certain where your boundary marks are, it’s a good idea to call a service that will come and mark your property lines with flags or spray paint before the fence is installed.
The next phase involves establishing the foundation of your fence by digging post holes. Once this is complete, your fence contractor will begin the process of constructing the bottom rail. This is where the fence begins to visibly take shape, and it’s important that each rail is firmly anchored to the posts and carefully aligned. During this stage, the professionals will also make sure there is an even gap between each plank to allow for expansion and contraction due to changes in temperature and humidity.
Once the bottom rail is securely in place, your fence contractor will begin to attach the horizontal rails to each of the line posts. This step is crucial for maintaining the structural integrity of your new fence and ensuring that each plank is evenly spaced. In addition, it’s a good idea to use a level to ensure that each rail is perfectly parallel to the ground.
Post-Setting
Once the fence area has been surveyed and the property lines marked, it’s time to put in your posts. Choosing the right material is essential for both long-term performance and aesthetics, so weigh your options carefully. Take into account installation costs and complexity, as well as possible maintenance, repair or replacement requirements. Also consider the impact on your home’s value and curb appeal – a cheap initial cost may actually end up costing you more in the long run.
A great option for wood fences is to use t-post clips. This will prevent the fencing wire from sliding up and down on the t-posts, or pulling away from them altogether. You’ll need a few clips for each strand of wire running between t-posts. Ask at your local Co-op for a complete supply.
For a longer-lasting, more sturdy fence post, you can also choose to set them in concrete. Be sure to take proper safety precautions when working with cement-based products, including eye protection and nitrile gloves. Dig a hole to a depth that is 1/3-1/2 the height of the post above ground level and fill it with pea gravel (larger aggregates will shift as they settle). Add QUIKRETE Fast-Setting Concrete up to the base of the post and add angled 2×4 braces on two adjacent sides, using a level to position each one plumb (perfectly vertical).
A handy product like Secure Set can save you a lot of time and effort by making it faster and easier to set posts. It works just like concrete, but you’ll be able to finish more projects in a day.
Rails and Panels
The rails and panels phase of fence installation involves building the vertical boards that create your final fence design. Your project team will guide you through your material options and show samples* to help you find the perfect look for your home. They’ll ask questions regarding homeowner association requirements, pet needs and your budget to make sure the fence you choose fits with your property and lifestyle.
Once your fence is installed, it’s important to conduct regular inspections to ensure that the structure remains safe and functional. This may include conducting visual assessments, testing post stability and checking for signs of damage.
Posts: Choose high-quality wood posts that are treated to resist rot and insect infestation. Depending on your preferences, select from cedar, pine or redwood. Ensure that the posts are straight and free from significant knots or defects.
Fence Styles: Pickets, lattice and chain link are traditional fence styles that provide privacy and security. Vinyl offers a low-maintenance option with the look of natural wood or stucco, and comes in multiple colors to match your home. Composite provides the durability of wood without the maintenance, and is available in a wide range of styles.
Check your fence for damage, such as warping or fading, and reapply any finish, if necessary. It’s also recommended to perform routine inspections after winter or rainy seasons, as excessive moisture can lead to rot or damage metal components.
Final Touches
Once the fence is built, it’s important to finish the project properly. Applying a sealant or stain protects the wood from moisture and UV rays, keeping it strong and looking beautiful for years to come. Regular inspections and reapplication of the coating will keep it in top shape.
Once line posts are set and concrete is in place, it’s time to attach the horizontal rails that will form the base of the entire structure. This step involves carefully nailing or screwing the rails to the posts and ensuring that they are parallel to each other. A level will be a big help to guarantee precise alignment and stability throughout the process.
After the rails are in place, it’s time to affix the panels to them. This is where the fence starts to take shape and can really add to its curb appeal. The panel slats should be firmly attached to the rails and secured with galvanized screws. It’s also a good idea to leave a consistent gap between each plank for proper expansion and contraction caused by temperature and humidity changes.
Proper preparation with the right tools and materials will ensure a smooth workflow and a beautiful finished product. By following these five essential steps, even the most novice do-it-yourselfer can achieve a functional and attractive fence that meets local zoning laws and property lines. Remember to check for any necessary permits before starting to avoid costly mistakes that may require the fence to be removed or altered.